The 10 Best 3D Printer Filaments
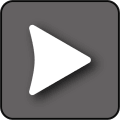
This wiki has been updated 32 times since it was first published in June of 2016. There's a huge variety of 3D printing filaments to choose from, and they're made using quite a few different materials, such as PLA, ABS, TPE, and PET. Their uses vary significantly and they're available in a wide range of colors, so we've tracked down some of the most useful and reliable 1.75-millimeter options. One of these choices should satisfy the needs of most users. When users buy our independently chosen editorial picks, we may earn commissions to help fund the Wiki.
Editor's Notes
April 07, 2021:
We haven't changed any of our recommendations here recently, and in a way, that illustrates the quality and sticking power of each item on our Wiki. In truth, the most important part to choosing your filament is what you'll be using it for and what materials your 3D printer can safely use. Practically speaking, you'll need to consider things like density, tensile strength, flexibility, and elasticity, and no single material can excel in all areas. Most, in fact, are pretty specialized.
In terms of looks, for many choices we've offered, there are usually alternative colors to choose from, with options like CC3D Silk and Amolen Glow in the Dark providing even more novel and memorable appearances. On the other hand, when you see something like the Yoyi TPU and eSun Elastic, which don't come in attractive colors or any alternate colors at all, it's a good sign that you're looking at a functional filament type rather than a decorative variety.
February 27, 2020:
There are a ton of different varieties of 3D printer filament to choose from, and they have quite a lot of differences aside from just color. The most common and easiest to use is represented here by eSun PLA+, which doesn't take a whole lot experience to use and is a highly versatile choice. If you're new to 3D printing -- or, for that matter, if you're concerned about harmful fumes -- this is the one to start with. Once you have a better plan of what you're building, you might want to move on to CC3D Silk or Amolen Colors Pack, although the Amolen can be a bit finicky. Like all three of those, 3D Best-Q Rosewood is also based on PLA, and despite its elegant appearance is actually pretty easy to use. Amolen Glow in the Dark is also based on PLA, and it's one of the few UV-reactive options that comes in blue, but it's not terribly bright on its own and it is, unfortunately, very expensive.
If you're looking for something with a little more structural strength, consider Hatchbox ABS. It smells terrible (and those noxious fumes aren't very healthy to breathe, either) but it's relatively easy to use and some people far prefer its results as compared to PLA. Overture PETG is another functional and versatile option, and it's one of the best food-safe choices out there; in fact, it's FDA-approved for use with culinary gadgets, as it's made from essentially the same material as single-use plastic bottles, but it's much more durable. As you might expect, though, it's not biodegradable, but it is recyclable in most places.
Then there are 3 we wanted to highlight because of their practical applications. Priline Polycarbonate is infused with carbon fibers and promises some of the best impact resistance out of everything we've outlined here. Overall, polycarbonate and carbon-fiber varieties tend to offer that. The main drawback to it is that it will destroy many nozzles, especially if they're made of brass. So it may require you to invest a little more in your equipment.
The last two we wanted to mention are in the TPE family. eSun Elastic is, as the name implies, highly elastic, and one of the most flexible overall. Yoyi TPU, on the other hand, is nearly as flexible but doesn't stretch, so it's suitable for things like R/C car tires and phone cases that need cushioning but can't be allowed to expand too much.
The Beginnings Of A New Technology
Actually, that's when a true 3D printing renaissance took place, beginning around when Hull's most important patents wore off in 2009.
The beauty of great science fiction is its basis in fundamentals that, while not necessarily real, are at least plausible. So, it takes a measure of creative talent, as well as incredible foresight, for the writers of mid-20th-century fiction such as Star Trek and The Jetsons to dream up fanciful machines that, just a half-century later, aren't actually so far from reality. Of course, we aren't quite on the verge of forming a balanced breakfast using a stockpile of free electrons, let alone printing lower-class citizens in The Fifth Element's bioprinting workshop. But in 2001, Jurassic Park 3 showed us a more realistic interpretation, when (spoiler alert) the protagonist saves the day using a replica velociraptor larynx formed from only schematics — a setup surprisingly comparable to where we're at today. But what exactly is 3D printing and how'd it come about?
The idea's been around since well before it reached the Starship Enterprise, and in 1981 a Japanese scientist named Dr. Hideo Kodama first began to explore it from a realistic perspective. With the technology to support his ideas still years away, the movement mostly languished until 1986. That's when American engineer Charles Hull filed a patent for a stereolithography apparatus, the first-ever machine to form a complete physical part based solely on a digital file. Chuck went on to found the 3D Systems Corporation, which continues to be a major industry presence in the modern era.
The field truly exploded in the early 21st century. While the general population was barely aware of it, the next chapter of building and creation was unfolding in the tech sector. Printers were designed that could print copies of themselves (or at least most of their components), and then robots took over the world. Just kidding. We hope. Actually, that's when a true 3D printing renaissance took place, beginning around when Hull's most important patents wore off in 2009. In the years since, the field has exploded, as engineering firms of all sizes continue to offer countless crowd-funded and corporate-backed designs, some of which are succeeding and some of which flopped fantastically. But one thing is certain: 3D printing is here, and it isn't going anywhere, aside from deeper into the fabric and infrastructure of our world.
How It Works
While it's rather new, and often used in advanced applications, 3D printing isn't too fundamentally complex. The most common varieties work a bit like a normal printer, laying down layer after layer of the appropriate material, all according to the programmed specifications. Every dimension and angle are charted as data that's translated to a physical space, much like a milling machine. The exact opposite of the milling process, however, printing adds material, whereas subtractive manufacturing carves it away.
While it's rather new, and often used in advanced applications, 3D printing isn't too fundamentally complex.
Typical stereolithography occurs as a light-sensitive liquid polymer is injected from a nozzle onto the machine's bed, where a UV field causes the photopolymer to take shape and solidify. This spraying and hardening repeats in layers until the entire object has been formed. A process called "slicing" involves scanning production-ready objects in three dimensions and digitally breaking them down into a multitude of individual, near-two-dimensional slices, which are then translated into the instructions needed for replication.
Another, more advanced type of machine involves a layer of medium, often a powdered substance similar to sand, which is kept at a specified depth across the machine's base as a laser focuses on the printing area. The laser reacts with the sand to form a solid compound, and once that entire slice is completed, the level of the floor underneath the sand is raised, and the next layer begun. This method works well for high-strength construction components, as metal must be dissolved and re-formed for maximum resilience.
What We're Doing With It
Just like the USS Enterprise was incapable of constructing the famed Romulan Ale, home cooks currently don't have access to a machine that instantly assembles food and drink at their request. But that's not to say that complex components of various types are out of reach. A few decades have been a lifetime for this fledgling technology, which is rapidly positioning itself as a building block of a more efficient, less stressful future.
But that's not to say that complex components of various types are out of reach.
In fact, one of the reasons the technology began to blow up in the early 2000s was its application within the medical field. Miniature human kidneys, cell-based blood vessels, and organically augmented prosthetics were among the revolutionary developments that spurred massive investment in the field just a couple decades ago. Some of these practices involving building mediums interspersed with bacteria, resulting in an actual, living ink to make up a newly constructed object.
Furthermore, consider the implications of machines that can build copies of themselves out of only the protons and electrons making up the objects around them. Someday, automatons will pre-assemble computers, structures, and even life support systems in situ while preparing for the arrival of humans at exotic, currently unknowable locations like Mars or the ocean floor.
Right now, at standard Earth gravity and atmospheric pressure, there are more than a few different substances used as 3D printer fodder. A readout of popular materials can be a serious alphabet soup: PLA, ABS, PETG, and TPU are some common plastics that see continued use. On the other hand, some projects call for specialized mixtures of metal, carbon-fiber, wooden, or the aforementioned bacterial inclusions, bonded by an oxygen-, ultraviolet-, or laser-hardened polymer.
A huge variety of filaments from which to choose means there's another intricate wrinkle that the enthusiastic engineer must explore, in order to come out with the highest quality components. Extrusion properties, melting points, structural rigidity, and even compatibility with a healthy human white blood cell are important considerations for many pioneers of 3D printing. With any luck, and a solid helping of human spirit and ingenuity, maybe someday engineers will create a real Replicator -- one that's even able to formulate authentic Romulan Ale.