The 9 Best Screw Extractor Sets
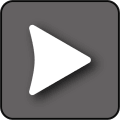
This wiki has been updated 33 times since it was first published in March of 2017. For most handypersons, professional contractors and mechanics, the occasional broken or stripped screw is impossible to avoid, but with one of these extractor sets, you don't have to stress about it. The options we've selected include tools that are capable of removing damaged or broken studs, bolts, and other fasteners, so you can spend more time getting on with the job at hand. When users buy our independently chosen editorial selections, we may earn commissions to help fund the Wiki.
Editor's Notes
November 17, 2020:
Today, the multipurpose Vampliers VT-001 comes on board, as a tool designed for extracting fasteners as well as cutting through or twisting wire. Their serrated jaws are made to bite into screw heads without slipping. You can have stubborn hardware removed in less time it would take to break out the power drill. Their bright rubber handles help them to stand out on your workbench, and they’re ergonomically designed and comfortable in the hand. They’re made with safety in mind, with a protective sheath you can slip over them when they’re not in use. They can handle stripped, rusted, corroded, or stuck screws, nuts, and bolts like a champ. For a more traditional set from a well-known name in tools, look to the comprehensive, 48-piece Irwin Hanson 3101010, each component of which sports a low profile that proves useful when you’re working in small spaces. With this set, you'll receive spiral flute, multi-spline, and bolt extractors as well as hard cobalt twist bits. The included left-hand cobalt drill bits come in handy for drilling out the interiors of fasteners. They come in a large, slotted blue case, so you can keep them organized with ease.
For a set of hex-head multi-spline extractors from the same manufacturer, consider the Irwin Hanson 53227, the stout shanks of which allow you to exert a high level of torque using a tap wrench or a drill. Their aggressive left-hand spiral design provides extra gripping power, so you can remove embedded studs, bolts, socket screws, and more. For a reliable set that works with a variety of types of fasteners, check out the Ridgid 35585. The set’s 24 components are made of tough steel for years’ worth of use, and they’re backed by a lifetime warranty. When you’re using a drill or other power tool for woodworking purposes, always wear protective eyewear for safety’s sake.
July 17, 2019:
If you work on machines and structures, the day will come when you'll be tightening a fastener and suddenly, it will give out and spin freely. This means that either it broke somewhere along its length or the head has been rounded. You'll have to dedicate time to removing it. Most mechanics carry small extractor sets like the Easy Out 63-65HRC or the Ontel SpeedOut. These work fine in many cases and can be used with a driver or tap wrench.
For tougher problems, the Irwin Hanson Master Set and the Ridgid 35585 provide the greatest versatility - including bolt removers that allow you to grip onto rounded bolt heads. These also include left-handed bits that will often be all that is needed. For the left-handed bits, a drill/driver works best as it provides the speed necessary for them to remove material efficiently. The spiral flute and multi-spline extractors work best when used with tap wrenches because it allows the greatest control of speed and torque while allowing you to use a hammer to lightly tap the extractor into the bolt hole. Using a drill with these tends to overspeed the extractors and not allow the spirals to dig into the bolt material. For bolt extractors, a long-handle ratchet or a regular ratchet with a cheater bar provides the best results and allows you to gain leverage over the bolt head while minimizing the chances of further rounding.
Extraction should always be performed with the aid of a penetrating oil. As a last resort, the entire bolt (along with the base threads) can be drilled out. Then, the new hole can be tapped and a wider fastener used. All mechanic and structural work should only be performed by trained technicians or tradesmen to avoid personal injury or damage to property.
Special Honors
DeWalt Max Impact Extractor Set Designed for use with both impact drivers and drills, this six-piece extractor set features reverse spiral flutes that help you remove fasteners from various types of material. They come in handy for removing damaged, rusted, or painted hardware such as hex screws, nuts, and bolts. With them, you’ll receive a 1/4-inch to 3/8-inch adapter. homedepot.com
The Fascinating History Of Fasteners
And while Archimedes' machines were important, they were hardly broken down into their most basic, fundamental components.
The first threaded screws are often traced to Plato's friend Archytas, though his were used to press olives and grapes. The great Archimedes drew up plans for a vertical, screw-based water pump, though his introduction of mechanical advantage was much more noteworthy. Ultimately, the Greek mathematician focused his machinery research on three implements: the lever, the pulley, and the screw.
Their first use as fasteners occurred in 15th-century clocks, with metal screws arriving in the late 1700s. Most earlier threaded designs were for pumps, and took incredible time and skill to craft by hand. In fact, if you take a close look at the Archimedean simple machines, you may notice that they're pretty complex for the supposed building blocks of all mechanics. After all, one's a fulcrum and an extension, another's a wheel rotating around an axle, and the third's a wedge, oriented on an inclined plane, wrapped around a fulcrum of its own, while a screwdriver serves as a lever.
Modern theory, however, attempts to classify machines by their truly most basic parts, called machine elements. And while Archimedes' machines were important, they were hardly broken down into their most basic, fundamental components. So, what are the elements that make this ubiquitous piece of hardware work so well?
More Than Just A Glorified Nail
Not to disparage the lever or wedge, but the idea of classical machines was an uninformed Renaissance reinterpretation of the same archaic natural philosophy that brought us the four humors, aether, and the existence of a being's quintessential form. In the 1800s, there was an established list of over 200 such elements, well before the climax of the Industrial Revolution. This was the birth of a new engineering discipline known as kinematics.
Rouleaux realized that many supposedly different machines operated on the same mechanical principle, and were differentiated mostly by how their components were connected.
In simplified terms, a kinematic pair consists of two rigid bodies that are joined together for mechanical purposes. The roots of modern machine theory came about in the mid-1800s courtesy of Franz Rouleaux, who based a revolutionary classification system on certain basic joint configurations, as well as drive connectors like chains and belts. Rouleaux realized that many supposedly different machines operated on the same mechanical principle, and were differentiated mostly by how their components were connected. Rather than a collection of parts connected by joints, kinematics views a machine as a group of fundamental, all-important joints that are connected by various rigid bodies.
Officially, a screw is a type of kinematic pair called a helical joint, referring to the helix shape formed by a screw's main point of contact with another object. According to our aforementioned tool-classifying guru Franz, the important part is the joint, and not the rigid components. Therefore, the key to the screw must be the friction applied to the sharp, spiral-shaped ridge running along the body. Those spiral ridges, called the screw's threads, are where all the power lies. The angle they cut into the material, the diameter of their spiral, and how tightly they're packed all affect the distribution of force and mechanical advantage gained while the fastener is turning clockwise. Once it's screwed all the way in, the static friction pressing against the threads keeps it tight, as does the friction between the material's face and the underside of the screw's head.
Unfortunately, every day there are good screws that fail to make it out of such high-pressure situations.
A Double-Edged Sword Called Friction
While they're all conceptually the same, there's a sizable number of styles of the indispensable fastener. There's the classic wood screw, with a simple, sharp tip that's ideal for biting into wood. Beefy, self-tapping varieties are meant to grind their way into especially hard materials, often without a pre-drilled hole. Drywall, decking, sheet-metal, and masonry screws all specialize in penetrating and securing their namesake material. There are many different profiles of head used for various purposes, and they feature one of several drive types such as flathead, Philips, hex socket, and star bits. Some screws also have hex heads for traditional socket drivers, simple knurled knobs, or no head at all.
Once a fastener is stuck, you can try using a different screwdriver to find a little remaining grip, or a couple knocks of a hammer to break it loose.
It usually takes more than friction to make a screw's resting place permanent. Lubricant, locking compound, and quality alloys can prevent fatal oxidation and corrosion. Using care to apply the proper amount of torque prevents galling, or cold-welding, from turning two pieces of healthy metal into one under extreme pressure. But the most common culprit is a stripped or rounded-off screw head. Using the wrong size wrench or driver, or using the tool at an improper angle can lead to this all-too-frequent problem.
Once a fastener is stuck, you can try using a different screwdriver to find a little remaining grip, or a couple knocks of a hammer to break it loose. But if it's in there for good, you have at least two options. The simplest method is to simply drill down the middle of the offending screw with a tempered steel bit. The remaining slivers of threads will crumble, and the fastener will no longer exist — except if you want to reuse the hole, you may have to spackle, fill, or re-tap it, depending on what it's made of. If you can access the bottom of the head, a Dremel tool or other small grinder will lop it right off, at least allowing you to disassemble your project. If neither of those options is viable, you might need a specialized extractor set.
Whether internal or external, the general concept of the most popular extractor variety is simple: reversed threads made of metal so sharp and hard that they slice counter-clockwise into the frozen screw and grip it with incredible pressure. The main differences between kits are the variety of sizes, the quality of the metal they're made of, and their warranties. The whole point of these is to absorb far more energy than normal. So, if you can find a lifetime warranty, it's definitely worth having. After all, over time, even the best of screws can falling victim to rust and thermal swelling.