The 9 Best MIG Welders
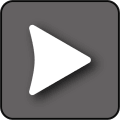
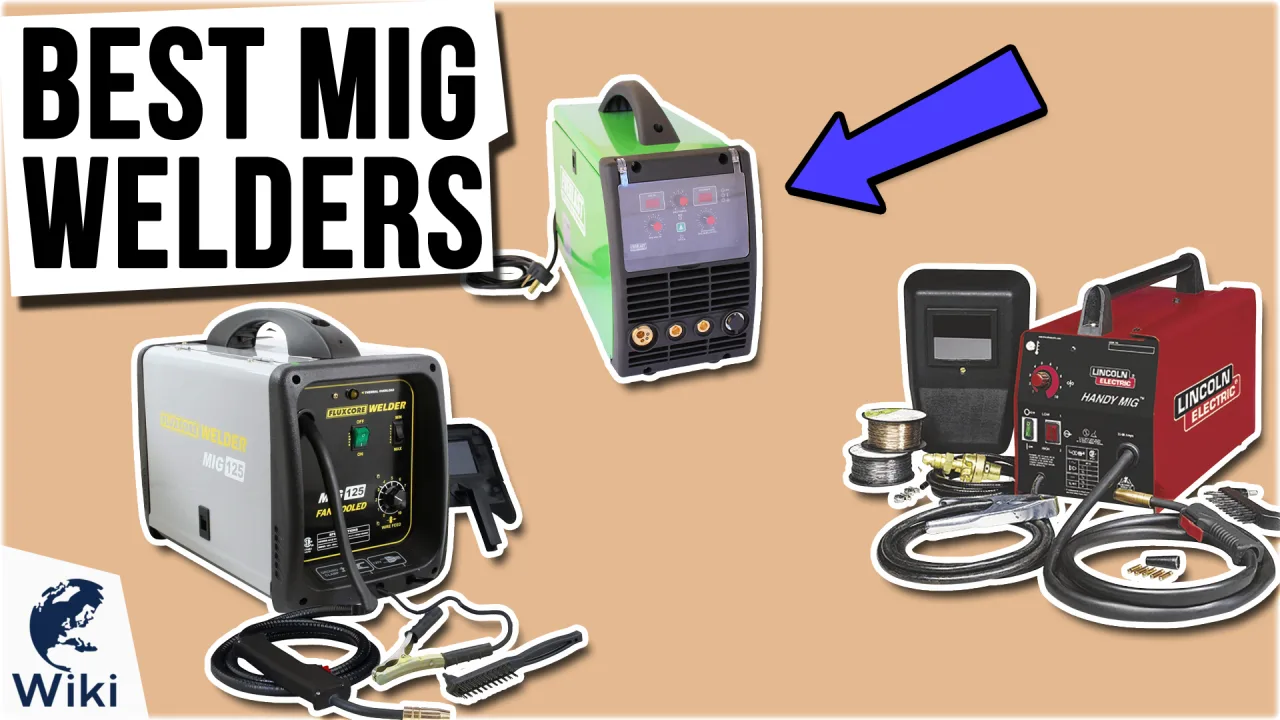
This wiki has been updated 44 times since it was first published in October of 2015. Metal Inert Gas (MIG) welding is easy to learn, requires virtually no cleanup, and allows for high productivity. Whether you are an automotive body worker, metal fabricator, or an artist, our selection of gear offers something for just about any type of project. We've included both 110 and 220-volt units, and models that handle flux wire welding. Always follow safety protocols to avoid injuries. When users buy our independently chosen editorial picks, we may earn commissions to help fund the Wiki.
Editor's Notes
May 20, 2021:
We made a couple subtle but important changes this time. This update saw the removal of a lesser-known brand called Longevity that ended up with poor availability and long-term reviews. We also needed to move on from a two-year-old Everlast model that's since been surpassed in quality and versatility by a similarly priced alternative. This new addition, the Everlast PowerMIG 200, is located in the middle of the price range yet offers a host of features normally reserved for very expensive units. Another reason it's worthy of your trust is its dual-voltage compatibility, which ensures it performs well in both consumer and industrial settings. You can spring for ultra-premium models like the Lincoln Electric K3068-1 if you'll be using it on a full-time basis, but for most users, the Everlast dual-voltage is the way to go.
January 01, 2020:
Removed the Campbell Hausfeld WG216001AV because of availability concerns and the Goplus Wolf 30 because of quality concerns. Added the Miller Electric 907321 and the Lincoln Electric K3068-1. The MIG welding needs for professional metalworkers will only be fully met by large machines like these with high-output amperages. Anything smaller won't weld thick plate and will periodically need to cool to avoid automatic shut downs or a decrease in performance.
Given that most will not need such high-performance machines, the Hobart Handler 190 takes the top spot for its excellent build-quality and relatively low cost. While you won't be welding any 1/2-inch stock, at 190 amps, most jobs can be handled with a couple of passes. Also importantly, the output speed and power can be easily and accurately adjusted to correspond to the material being welded.
Welding is extremely dangerous because of the high voltage used, high-intensity light rays produced, and with MIG welding in particular, the pressure vessels used. Always use both skin and eye protection, along with proper grounding practices to avoid personal injury.
Special Honors
Miller Electric Deltaweld 500 This pulse-MIG capable model offers a wide operating range for every wire diameter along with less fumes, less spatter, and less heat warping than non-pulse welders - this all translates to very high-quality welds that will require very little clean-up. millerwelds.com
Go MIG Or Go Home
True craftsmanship in the age of mass production is a rare thing, but that doesn't mean it's particularly difficult for you to get the hang of it.
You may have noticed the sometimes awfully crude joints between metal pieces on the furniture you've purchased through the years. I know I've assembled a few pieces from a certain Swedish manufacturer the welds of which could be pulled apart with a little elbow grease. True craftsmanship in the age of mass production is a rare thing, but that doesn't mean it's particularly difficult for you to get the hang of it.
MIG welding is a fast, relatively easy welding method to learn, and it's pretty safe compared to other methods available. Let's break down the name before we go any further.
MIG stands for Metal Inert Gas, and it refers to the inert gas that flows from a tank separate from the welder, through the welding hose, and out the tip of a welding gun into the immediate vicinity of your weld. The presence of the gas–usually argon or a mixture of argon and carbon dioxide–keeps other gasses in the space like oxygen or water vapor from getting into the weld area, gasses that would reduce the quality of the weld.
Also sticking out of the end of the welding gun, at the end of the hose is the tip of a long wire, the material of which will change with whatever metal you intend to weld. That wire acts as a positively charged anode, and if you follow it back through the hose and into the welder housing, you'll find a big replaceable spool of it there.
Running out the other end of the welder housing is a clamp that greatly resembles the clamps you use to give your car a jump start off another car's battery. This clamp acts as the negatively charge cathode, and in order for your weld to work you have to either clamp it to the piece you intend to weld or to the table on which you're welding.
When you fire up the welder and bring the tip of the anode wire as close to the metal joint as possible, an electric arc forms the completion of the short circuit. The tremendous heat that this arc creates melts the intended metal, which immediately cools into its new shape and fusion when you let go of the trigger on the welding gun.
Power And Flux
Selecting from among the MIG welders on our list has as much to do with your experience level as a welder as it does with what materials you intend to weld. Since you're investigating MIG welders, it's safe to assume you have a shop or a garage in which you plan to work.
The 110V options are less powerful, to be sure, but for light work and a new welder these might be your best bet.
Some of the welders on this list operate from a standard 110V outlet, while others require a 220V connection. The 110V options are less powerful, to be sure, but for light work and a new welder these might be your best bet. There are other models on our list that actually have built-in transformers to take your 110V outlet and upcharge it to 220V.
If you're just getting started, but you know you want to be in it for the long haul, a transformer-based model will allow you to learn without changing anything about the electrical layout of your home. It's also a good idea, if you're just starting out, to see which welders on our list come with complete kits, including wire options, a shield, and a gas hook-up.
Speaking of gas, there's an option in MIG welding that bypasses the need to connect your welder to a tank of inert gas, an option that some of the welders on our list can handle. It's called flux core, and it's a bit of a double-edged sword. Flux core is essentially a hollow wire with a flux running through its center. When exposed to the heat of the weld, this flux converts into the shielding gas required to keep the weld clean.
The upside to flux core welding is that you don't need to lug around a big tank full of argon to get a job done, and it allows you to work outdoors in settings that otherwise would have necessitated a more traditional arc weld. The downside is that it can be a little smoky to operate, and the gas created by the flux doesn't keep the weld as clean as the flow from a tank will.
A Historical Arc
Early developments in arc welding corresponded to early developments in electricity. It seems as though, while men like Thomas Edison and Nikola Tesla were trying to make electricity safer and safer, other scientists and engineers, like Nikolay Slavyanov were busy finding ways to use the dangerous aspects of electricity to an industrial advantage.
Early developments in arc welding corresponded to early developments in electricity.
In 1920, arc welding methods began to gain some popularity thanks to the efforts of P.O. Nobel of General Electric, who used a direct current through a bare electrode to produce a weld in the absence of any shielding gas.
The use of inert gasses to curate a more conducive welding atmosphere wouldn't enter the picture until 1948, when the Battelle Memorial Institute, an Ohio-based charitable trust funding developments in the sciences, put forth the technology. The use of the inert gasses of the day was cost-prohibitive, however, so it failed to catch on an industrial scale.
In 1953, welders began to use carbon dioxide as the gas for their welding atmospheres, and since that development very little has changed in the methodology, with the notable exception of the development of flux core wire.