The 9 Best Arc Welders
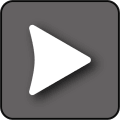
This wiki has been updated 35 times since it was first published in October of 2015. Anyone working with metal, from construction workers to sculptors, can use this list of stick welders to find the perfect model for their needs. Offering more versatility than gas-shielded processes, shielded metal electrodes don't require unwieldy gas tanks, can be used almost anywhere including residential and professional spaces, and are capable of working with most common metals and alloys. When users buy our independently chosen editorial picks, we may earn commissions to help fund the Wiki.
Editor's Notes
February 19, 2021:
We did remove a model from a lesser-known brand because it was somewhat unreliable and also discontinued, but otherwise, there have been few advancements in arc welder technology in the past couple years. One upgrade we did make is to the newest version of the Everlast PowerArc 210STL. It, and the Hobart 500570 Stickmate, are worthwhile options for a variety of purposes that won't break the bank, while the Hobart 500502 Stickmate is a slightly more expensive and versatile model with more power and the ability to handle wider sticks. For the slimmest of budgets, though, it's hard to beat the Amico Power, which is compact, lightweight, and reliable, although not intended for full-time use.
On the other hand, if cost isn't a huge concern, we highly recommend the Lincoln Electric K1297 if you have a 230-volt circuit or need DC operation, and the Lotos LTPDC2000D if you only have a standard, 110v connection and need something with impressive cutting power and a long duty cycle. Similarly, the Everlast PowerTIG and Lincoln Electric AC-225 are both high-end optionsd that are safe for all-day use, plus their straightforward and reliable controls make them ideal for intermediate metalworkers.
December 20, 2019:
Removed the ESAB Thermal and the Hobart Stickmate LX 235 because of availability concerns. Added the Lincoln Electric AC-225 and the Hobart 500502 Stickmate.
The AC-225, known affectionately as "the Tombstone", has performed reliably for generations of welders. It can be used to effectively weld 16 gauge steel and thicker and is perfect for novice metalworkers. It has a wide margin of error but, as many seasoned welders will tell you, its best to learn how to weld on stick before moving on to MIG or TIG. This is because stick has a higher learning curve involving lateral speed adjustments, amperage control, and arc length maintenance. Learning these skills will end up making other welding systems very easy to pick up.
When selecting a welder, it's important to note the needs of the machine. Some will run on standard 110 circuits but in addition to that will require a certain amount of current. In most cases, you'll need to run the welder on at least a 50 amp breaker. It's not enough to simply switch out the breaker at the box - usually, the wire gauge is selected to correspond to the current limit of the original breaker. This means that if a circuit has a 20 amp breaker, its very likely that the wire installed is meant to operate at or under 20 amps. So if you replace a 20 amp breaker with a 50 amp breaker, it's very likely that you'll have to upgrade the wire gauge to avoid causing a fire.
Welders are extremely dangerous because of the high current, voltage, and bright uv rays. Always use eye and skin protection, along with proper grounding to avoid personal injury.
Special Honors
Lincoln Electric Welding Equipment If your job demands top-of-the-line equipment, this popular manufacturer is a great place to start. In fact, if you need a specialized unit for underwater, engine-driven, or advanced process use on unconventional materials, they're truly an industry leader with products that are hard to beat. You will spend quite a bit to get something advanced, but you can be certain that it will last for years of professional use. lincolnelectric.com
Evolution Of Arc Welding
Other innovations in arc welding of the time include the use of a three-phase electric arc and an alternating current power source.
The first successful arc weld was performed in 1881 when Nikolai Benardos, a Russian inventor, displayed an arc welding of metals at the International Exposition of Electricity in Paris. He used a carbon electrode and, working with Polish inventor Stanislaw Olszewski, patented the carbon arc welding method.
Also in 1881, Auguste de Méritens, a French electrical engineer, discovered and patented another method for carbon arc welding. In the late 19th century, numerous advancements were made in arc welding. Metal electrodes were created in 1888 and, in 1900, coated metal electrodes were created, producing a more stable arc. Other innovations in arc welding of the time include the use of a three-phase electric arc and an alternating current power source.
From the 1920s to the 1960s, there was rapid development in arc welding methods. Automatic welding, which utilized a continuously fed electrode first started in the mid 1920s. Around that same time, scientists also began looking for ways to shield molten metal in welds from nitrides and oxides in the atmosphere, which can cause structural defects, namely brittleness and porosity. This led to the development of gas shielded arc welding. In 1930, the submerged arc welding method was created and in 1941, tungsten arc welding was finally perfected after decades spent trying to develop the technique.
Different Forms Of Arc Welding
Arc welding is the most common form of welding, and is also one of the most varied. It makes use of the concentrated heat created by an electrical arc to fuse metals. There are six different methods for arc welding that are popular today.
Shielded metal arc welding, or SMAW, is the oldest, and most basic form of arc welding. It is also the most versatile. As the electrode, sometimes called a welding stick, is touched to and removed from the working material, its tip is melted and becomes the material that forms the weld. Nitrides and oxides in the air can become integrated in SMAW welds and must be removed after each pass of the stick otherwise the integrity of the weld can be affected.
It requires more expertise from the welder, but can also make cleaner welds which need less finishing work.
Gas metal arc welding, also known as GMAW and MIG welding, makes use of gasses like helium or argon to shield the molten metal from the oxides and nitrides in the air. GMAW welding creates relatively low temperatures and it is best for thin sheet metal welds.
Gas tungsten arc welding, also known as GTAW and TIG welding, uses a tungsten electrode and also makes use of helium or argon to shield the weld from oxides and nitrides. In TIG welding, the electrode is not consumed as it is in other arc welding methods. This allows it to be used to create autogenous welds. It requires more expertise from the welder, but can also make cleaner welds which need less finishing work.
Flux-colored arc welding, or FCAW welding, makes use of electrodes that are filled with flux. This works to protect the molten metal from the nitrides and oxidizes in the same manner as gasses are used in other arc welding methods. It creates a higher weld-metal deposition rate, making it ideal for welding thick metals.
Plasma arc welding, or PAW welding, utilizes ionized electrodes and gasses to generate hot jets of plasma, which are aimed at the weld. These super hot plasma jets are extremely concentrated allowing for faster and deeper welds.
Submerged arc welding, or SAW welding, also uses a granular form of flux. As the weld is performed, the flux gets fed into it, forming a protecting layer that prevents spatter and sparks. Like PAW welding, it can also be used when deeper welds are required, but it is limited to horizontal welds.
Safety Tips For Arc Welding
Welding should always be performed in well ventilated areas. To keep an area safe for breathing, welding fumes should be kept below 5mg per cubic meter of fresh air. This low threshold, can be reached very quickly if sufficient ventilation is not provided. Always perform welds in open spaces. If a welding must be done in a confined area, a fume mask and an air-fed helmet should be worn.
If a welding must be done in a confined area, a fume mask and an air-fed helmet should be worn.
Welding also creates dangerous levels of ultraviolet light and infrared rays. If one is not properly protected they can cause a sun-burn like effect on the skin and photokeratitis or cornea burns to the eyes. To prevent this, always wear a welding helmet, welding gloves, and clothes that provide a large amount of skin coverage.
Arc welding creates a large amount of sparks and spatter. The more inexperienced a welder is, the more sparks that will be created. While not dangerous in the long term, it can be extremely annoying when trying to concentrate on the job at hand. Thick clothing and a welding cap that covers the neck can help reduce the annoyance from sparks and spatter. Because of the large amount of sparks arc welding produces, the immediate area should also be cleared of any flammable liquids or materials. A fire extinguished that contains CO2 or dry powder should also be kept readily accessible.
Even after the weld is completed, one should not look at it closely with unprotected eyes until it has fully cooled. During the cooling period, welds contract and can throw off pieces of slag, which can burn the eye.