The 10 Best Die Grinders
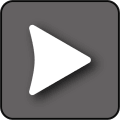
This wiki has been updated 34 times since it was first published in October of 2016. When you need something to take the edge off — and you mean that literally — you'll want to reach for one of these die grinders. Each unit boasts unique features and combinations of utility, so you're sure to find one that works perfectly for your specific needs. We've included both heavy-duty options suitable for removing stock and taking off rust to smaller models ideal for fine polishing. When users buy our independently chosen editorial selections, we may earn commissions to help fund the Wiki.
Editor's Notes
June 10, 2021:
Without any recent major changes to the industry, all our die grinder recommendations remain the same. Of course, it's worth noting that while there are some great electric models out there, such as the Makita GD0601 and DeWalt DWE4887 that can both run on either AC or DC power, you'll get by far the best performance out of an air-powered model. For that, you'll generally need a relatively powerful air compressor, as handheld compressors won't cut it, and even many pancake compressors lead to prohibitively short duty cycles.
January 23, 2020:
Removed the Dremel 8220-2/28 because of availability concerns. Added the Aircat 6260.
While the word 'die grinder' tends to be used to refer to pneumatically powered rotary tools, it technically includes light-duty electric rotary tools as well. That, along with the fact that it is quite difficult to draw a sharp distinction between the two styles other than the power source led us to include both electric and pneumatic models.
Both the Chicago Pneumatic CP860 and the Aircat 6260 are excellent options with great performance. Both use direct drive mechanisms to transfer the power of the motor to the collet without sacrificing speed. This is opposed to the angled gear mechanism of models like the Ingersoll Rand 301B which introduce the possibility of gear binding if they are not properly lubricated.
If you don't have access to compressed air, you might consider either the DeWalt DWE4887 or the Makita GD0601. Both are well-made, however, there is a justified concern about both using brushed DC motors instead of brushless DC motors given that die grinders are 'continuous operation' tools. We can reliably predict that frequent users will need to replace the brushes quite often.
Air compressors and die grinders are inherently dangerous. Use caution when using either to avoid personal injury.
A Brief History Of Power Tools
From manufacturer C & E Fein in 1895, the first powered drill was a cumbersome, nearly 20-pound monstrosity.
The way humans interact with the world around us largely separates us from the rest of the animal kingdom. Whether it's our ability to comprehend symbols and express them with words, or our capacity for abstract thinking, it's easy to see that our mental faculties are rivaled by few, if any other species on Earth.
Another characteristically human activity is advanced tool use. Lots of animals, including various mammals, birds, crocodilia, and fish use relatively simple tools, but only homo sapiens are known for developing complex machines. In fact, tool use is so integral to human existence, that the names of three major time periods — the Stone, Bronze, and Iron Ages — correspond to the principal ingredients in the alloys used to make the era's tools.
Over 5,000 years ago in the fertile crescent, the Mesopotamians first employed the wheel as a tool for making pottery. Stone wheels have long served to grind grain into flour, and around the year 2100 B.C.E., the Egyptians developed a mechanically driven lathe that resembled an ancient bench grinder, variations of which would sharpen tools for thousands of years to come.
Not long after Thomas Edison lit up Menlo Park, some industrious engineers combined the newly popular electricity with familiar hand-powered tools. From manufacturer C & E Fein in 1895, the first powered drill was a cumbersome, nearly 20-pound monstrosity. Two decades later, Duncan Black and Alonzo Decker collaborated to combine an electric motor with the grip and trigger style of the wildly popular Colt handgun, and in 1916 Black and Decker released the first power drill to the public.
Also around the dawn of the 20th century, engineers developed silicon carbide and aluminum oxide, two synthetic grains that revolutionized the abrasives industry that the Chinese had started 600 years earlier using tree gum and crushed seashells. Innovative craftsmen then combined wheels, electricity, and abrasives to create the die grinder, one of the most versatile and popular tools today.
Always On The Grind
Die grinders exist for intricate, exacting jobs that call for large amounts of power. They're small and light enough to easily maneuver around tight spaces and small components, whether you're sitting at a workbench or shaping fittings on the job site. Aside from their size, die grinders are effective thanks to their incredibly high speeds and their abrasive nature.
Coated abrasives, on the other hand, adhere to the outside of the bit.
While the teeth on a traditional saw can easily rip through wood, many other materials require a different approach. To cut extremely hard substances like metal or masonry, you'll need a fast motor and a resilient cutter. There are some toothed options for slicing through stone and steel, but they require stationary chop saws and result in relatively rough edges. The most popular and effective way to power through exceptionally hard items, especially smaller ones, is with a cut-off wheel or abrasive bit, of which there are two main types.
Bonded abrasives consist of rough particles joined together with solid clay, resin, or silicate such as glass. They're inexpensive, because they continually erode during use. While that means each bit has a relatively short lifespan, it ensures there's always a clean surface and consistent grit doing the work. Coated abrasives, on the other hand, adhere to the outside of the bit. For high-speed use, these coatings must be made of a superabrasive that's tougher than what they're grinding. The most common superabrasive is synthetic diamond, though other advanced grains are available. These compounds don't wear away like the bonded ones; instead they get extremely hot, which can smooth them out and even cause them to crack and shatter. Most craftsmen use a wet technique with superabrasive attachments, because the lower temperature and longer life makes for easier work and cleaner results.
Power Versus Pressure
Different grinders have different power plants, mostly depending on their size. Some of the smallest, including many of the well-known Dremel models, use relatively simple, carbon-brushed DC motors, which get the job done on a small scale. Larger models often use universal motors, so called because they're technically able to run on AC or DC power. These can spin considerably faster than commutated motors, which is critical for a tool that makes in the neighborhood of 30,000 revolutions each minute.
These can spin considerably faster than commutated motors, which is critical for a tool that makes in the neighborhood of 30,000 revolutions each minute.
Electric models are popular for smaller tasks and among DIY enthusiasts, but the pneumatic die grinder is far more common in professional situations. Like with other air-powered tools, they're remarkably strong, and they have incredible torque, instant spin-up, and the convenience of interoperability with huge numbers of other tools. Plus, they're far more durable and less expensive. The main drawback to pneumatics is that they're tethered to a compressor, and not only are those quite loud, they generally require a 120V AC connection or better. Also, they add an additional piece to the equation; one that calls for care and maintenance like any other high-powered machine. Any shop responsible for high-volume metalwork should definitely consider an air-powered option, while electric grinders are suitable for many home and hobby applications.
All power tools require the proper respect and maintenance; dull and poorly maintained implements are exponentially more risky, and good upkeep usually isn't too difficult. Die grinders, specifically, call for extreme care during use, as it may only take one missed cut to jerk a cutting disk sharply in one direction. To that end, make certain that your work space is clean, clear, and free of flammable materials. Be aware of your project's immediate surroundings; it takes a die grinder a fraction of a second to rip through a brake line or electrical wire, either of which could spell disaster. If you're operating on smaller items, make sure they're firmly held down. Always use eye protection, and gloves are an excellent idea, as well. As long as you follow safety precautions and pay close attention to the job at hand, the right die grinder can make life in your workshop quite a bit easier.